余姚市优职模具厂
1.0模具的结构组成
依据模具中各个部件的不同效果,一套模可以分红以下几个部分:
1)内模零部件,赋予成型材料形状和尺度的零件。通常由下模上模,镶件(镶针)等组成。
2)浇注体系:将熔融塑料由机射嘴引向闭合的模腔,一般由灌口干流道、分流道、浇口和冷料穴组成。
3)热交换体系:为了满足成形工艺对模具温度的要求(冷却或加热)需要对模具温度进行较准确的调整。
4)行位体系:当侧向有凸凹及孔时,在塑料被顶出之前,必须先抽拔侧向的型芯(或镶件),才能使塑件顺利脱模。
5)顶出体系:实现塑件脱模的机构,其结构形式许多,常用的是顶针、司筒和推板等脱模机构。
6)导向定位部件,是保证动模与定模闭合时能准确对准、脱模时运动灵敏,时接受侧向力的部件,常由导柱和导套及定位块、锥等组成。
7)排气体系:将型腔内空气导出的排气槽及空隙
8)结构件:如模架板、支承柱、限位件等。
2.0模具规划的基本程序
2.1规划模应考虑的问题:
1) 剖析塑件结构及其技能要求。要注意塑件的尺度精度、表面粗糙度的要求及塑件的结构形式,对不合理的结构要提出改善塑件规划的建议。
2) 了解机的技能标准。包含锁模力、容模量,开模间隔、顶出孔大小位置和数量、码模方法、法兰尺度及其它机器参数。附表(积丰现有的注塑机)
3) 了解塑件材料的加工性能和工艺性能,包含塑件能到达的流动间隔比;塑料在模具内或许的结晶、取向及其导致的内应力;塑料的冷却缩短和补缩;塑料对模具温度的要求等。
4)了解特别技能要求。
5) 考虑模具的结构和制作,包含选择分型面和型腔的安置及进料点;模具的强度、刚度和模腔尺度精度;行位机构和顶出体系;模具零件的制作方法及制作的科学性可行性及经济性;装拆的工艺性;必要的辅助工具的规划等。
6) 考虑模具材料的选择,包含材料的机械、工艺性能及热处理要求,材料胚料的大小。
7) 考虑模具的成型效率,合理的设置运水。
3.0模具规划的一般流程
1)1.模具承认表-总目标:交货期,模具寿命。
2.塑胶件:材料,表面质量,几许形状,其他要求。
3.机:型号标准。
4.行腔数目
5.行腔排布,模架确定、
6.分型面、
7.塑腔尺度
8.主浇道以及分流道
9.浇口
10.冷却体系
11.结构件规划
12.行腔准确尺度
13.顶出体系
14.导向定位体系
15.排气体系
16.装置选件
2)对流程图的阐明:
流程图只阐明了在模具规划过程中考虑问题的先后顺序;而在实践的规划过程中或许并不是按此顺序进行规划的。而且规划中常常要再回来上步或上几步对已经的规划步骤进行修正,直至终究决议规划。
4.0模架、内模材料的订制程序
1.主管
2.收到产品图 承认表
3.剖析产品结构,模具规划要求
4.(1)复杂,组织画模具排位图
(2)简略,画模具结构简图
(3)客户要承认结构。 组织规划 客户承认。订料,调整规划
5.简略和复杂。 订模架。内膜大料。组织规划
6.之后审图
7.出图纸 明细表。

表2-4
塑料名称 型腔斜度 型芯斜度
聚酰胺(尼龙)PA 25ˊ-40ˊ 20ˊ ~ 40ˊ
聚乙烯PE 25ˊ-45ˊ 20ˊ ~ 45ˊ
聚苯乙烯PS 35ˊ~ 1°30ˊ 30ˊ ~ 1°
聚甲基丙烯酸甲酯PMMA 35ˊ~ 1°30ˊ 30ˊ ~ 1°
ABS 40ˊ~ 1°20ˊ 35ˊ ~ 1°
聚碳酸酯PC 35ˊ~ 1° 30ˊ ~ 50ˊ
聚甲醛POM 35ˊ~ 1°30ˊ 30ˊ ~ 1°
热固性塑料 25ˊ~ 1° 20ˊ ~ 50ˊ
从模具结构和制造析,塑件的结构要具备以下特点:
1) 塑件要有足够的拔模角,以利于塑件从模腔及模呵上脱出,(表2-4)是塑件的单边脱模角的推荐值。蚀纹表面的脱模角要大。
2) 钩、扣位工艺孔
塑件的钩位、扣位等结构有些是通过前后模插穿实现的。
3) 落在曲面上的孔,孔口要倒角,以避免出现尖锐的胶位。
4) 用Half成型外螺纹或精密圆柱时,要削平与PL面垂直的两个面
5) 当内、外螺纹必须采用旋转脱模时,应合理的设置止转位
6) T形切面的接合面会产生凹陷,要在模呵(core)侧边设置锲角减薄胶位
7) 加强筋高度的预留
8) 一般的,塑件上注有公差的尺寸,在计算收缩时,要取中间尺寸为名义尺寸。
9) 当塑件使用的塑料收缩率变化范围较大时,如果塑件的尺寸公差要求小于可能出现的收缩变化,模具上要留有可修改的量,考虑能镶、能换,做一些防错应变措施。
10)要对大于基本胶厚的部分作吊空胶处理,保证基本肉厚一致,并考虑冷却问题。
11)面壳比底壳预大的问题。通常要求:
面壳周边大出约0.03 ~ 0.05。但底面壳缩水可能不一样。拿遥控器面壳来说,由于胶厚、模温、产品形状与底壳有差异,造成面壳收缩率大于底壳,这在尺寸预留时要预以考虑。加胶要加易修正的壳。
12)上、下模有胶位时要考虑预留。如上模出圆角、倒角时,一般下模胶位要多单边0.03 ~ 0.05。
13)变形的预留:
a 反变形
b 吊空胶
6.0绘制模具图
6.1 模具总装图包括以下内容:
a. 模具成型部分结构
b. 浇注系统、排气系统的结构形式。
c. 分型面及分模取件方式。
d. 外形结构及所有连接件,定位、导向件的位置。
e. 标注型腔高度尺寸(不强求,根据需要)及模具总体尺寸。
f. 按顺序将全部零件序号编出,并且填写明细表。
6.2绘制零件图
由模具总装图拆画零件图的顺序应为:先内后外,先复杂后简单,先成型零件,后结构零件。
a. 图形要求:一定要按比例画,允许放大或缩小。视图选择合理,投影正确,布置得当。易看懂、便于装配,图形尽可能与总装图一致,图形要清晰。
b. 标注尺寸要求统一、集中、有序、完整。标注尺寸的顺序为:先标主要零件尺寸和出模斜度,再标注配合尺寸,然后标注全部尺寸。在非主要零件图上先标注配合尺寸,后标注全部尺寸。
c. 表面粗糙度。把应用多的一种粗糙度标于图纸右上角,如标注'其余3.2。'其它粗糙度符号在零件各表面分别标出。
d. 其它内容,例如零件名称、模具图号、材料牌号、热处理和硬度要求,表面处理、图形比例、自由尺寸的加工精度、技术说明等都要正确填写。
6.0审图程序(设计人员先按表自审,然后交主管审图)
分 类 校 核 事 项
1.品质 充分检讨型模材料,硬度,精度,构造等是否与定制者之规格相符?
2.成形品 检讨缩水,材料流程,等诸事项是否影响成形品外观?在成形品之机能及构造无故障范围中,检讨型模加工是否容易?成形品材料之收缩率是否估计正确?
3.成形机 成形机之射出量,射出压力,合模压力是否充分?型模是否能正确安装于指定使用之成形机上。亦即,装接螺丝位置,定位环之位置,喷嘴半径R,注嘴孔径,顶出用孔位置及大小,型模大小及厚度等是否适当?固定板压板位有铣薄至跟动模固定同厚。
4.基本构造
(1)顶出机构 选用之顶出方法对成形品是否适当?顶针、顶板、司筒、气顶,其它等。顶针、司筒(尽量大些、顶在骨上)使用数量及位置是否适当?有无必要做三个顶辊孔?司筒有无碰顶辊孔?行位下边有顶针时,顶针板有无加行程开关?有斜推针时,顶针是要加“+”字槽防滑,有否加顶针板行程开关?
(2)温度控制 运水大小,数量,位置是否适当?有无标注喉牙规格?有无撞顶针等?
(3)行位 行位机构是否合适而确实?较大行位有无加铲鸡面垫板?用波子螺丝还是定位?
(4)流道·浇口 有无按要求设计流道系统?多腔模具是否入水均匀?

1.0注射模具的结构组成
根据模具中各个部件的不同作用,一套注射模可以分成以下几个部分:
1)内模零部件,赋予成型材料形状和尺寸的零件。通常由下模上模,镶件(镶针)等组成。
2)浇注系统:将熔融塑料由注射机射嘴引向闭合的模腔,一般由灌口主流道、分流道、浇口和冷料穴组成。
3)热交换系统:为了满足注射成形工艺对模具温度的要求(冷却或加热)需要对模具温度进行较精确的调整。
4)行位系统:当侧向有凸凹及孔时,在塑料被顶出之前,必须先抽拔侧向的型芯(或镶件),才能使塑件顺利脱模。
5)顶出系统:实现塑件脱模的机构,其结构形式很多,常用的是顶针、司筒和推板等脱模机构。
6)导向定位部件,是保证动模与定模闭合时能准确对准、脱模时运动灵活,注射时承受侧向力的部件,常由导柱和导套及定位块、锥等组成。
7)排气系统:将型腔内空气导出的排气槽及间隙
8)结构件:如模架板、支承柱、限位件等。
2.0模具设计的基本程序
2.1设计注射模应考虑的问题:
1) 分析塑件结构及其技术要求。要注意塑件的尺寸精度、表面粗糙度的要求及塑件的结构形式,对不合理的结构要提出改进塑件设计的建议。
2) 了解注射机的技术规格。包括锁模力、容模量,开模距离、顶出孔大小位置和数量、码模方式、法兰尺寸及其它机器参数。附表(积丰现有的注塑机)
3) 了解塑件材料的加工性能和工艺性能,包括塑件能达到的流动距离比;塑料在模具内可能的结晶、取向及其导致的内应力;塑料的冷却收缩和补缩;塑料对模具温度的要求等。
4)了解特殊技术要求。
5) 考虑模具的结构和制造,包括选择分型面和型腔的布置及进料点;模具的强度、刚度和模腔尺寸精度;行位机构和顶出系统;模具零件的制造方法及制造的科学性可行性及经济性;装拆的工艺性;必要的辅助工具的设计等。
6) 考虑模具材料的选择,包括材料的机械、工艺性能及热处理要求,材料胚料的大小。
7) 考虑模具的成型效率,合理的设置运水。
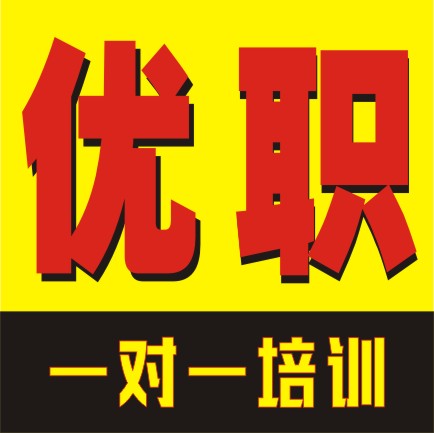
![]() |